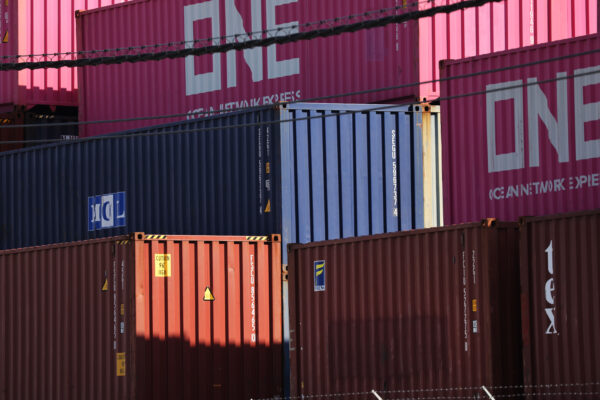
Ah, the unassuming shipping container. It’s really nothing more than a big steel box with a couple of doors. At any given time, millions of containers are piled on ships plying the world’s waterways. Battered by weather and waves, they are packed with just about anything you can imagine — exotic fruits and vegetables, cheap clothing and electronics, parts for cars and trucks.
“Globalization, as we know it today, would not have been possible without the container,” says Marc Levinson, an economist, a historian and the author of two books on shipping containers.
These days during the coronavirus pandemic, with the holidays fast approaching, jampacked container ships have gotten stuck in traffic at ports, which is choking the economy. Delayed containers have become both a symptom of and a contributor to global supply chain problems. But if one looks back, cargo has generally moved more easily and cheaply now than it did before these big boxes came around, making them almost indispensable to the global economy.
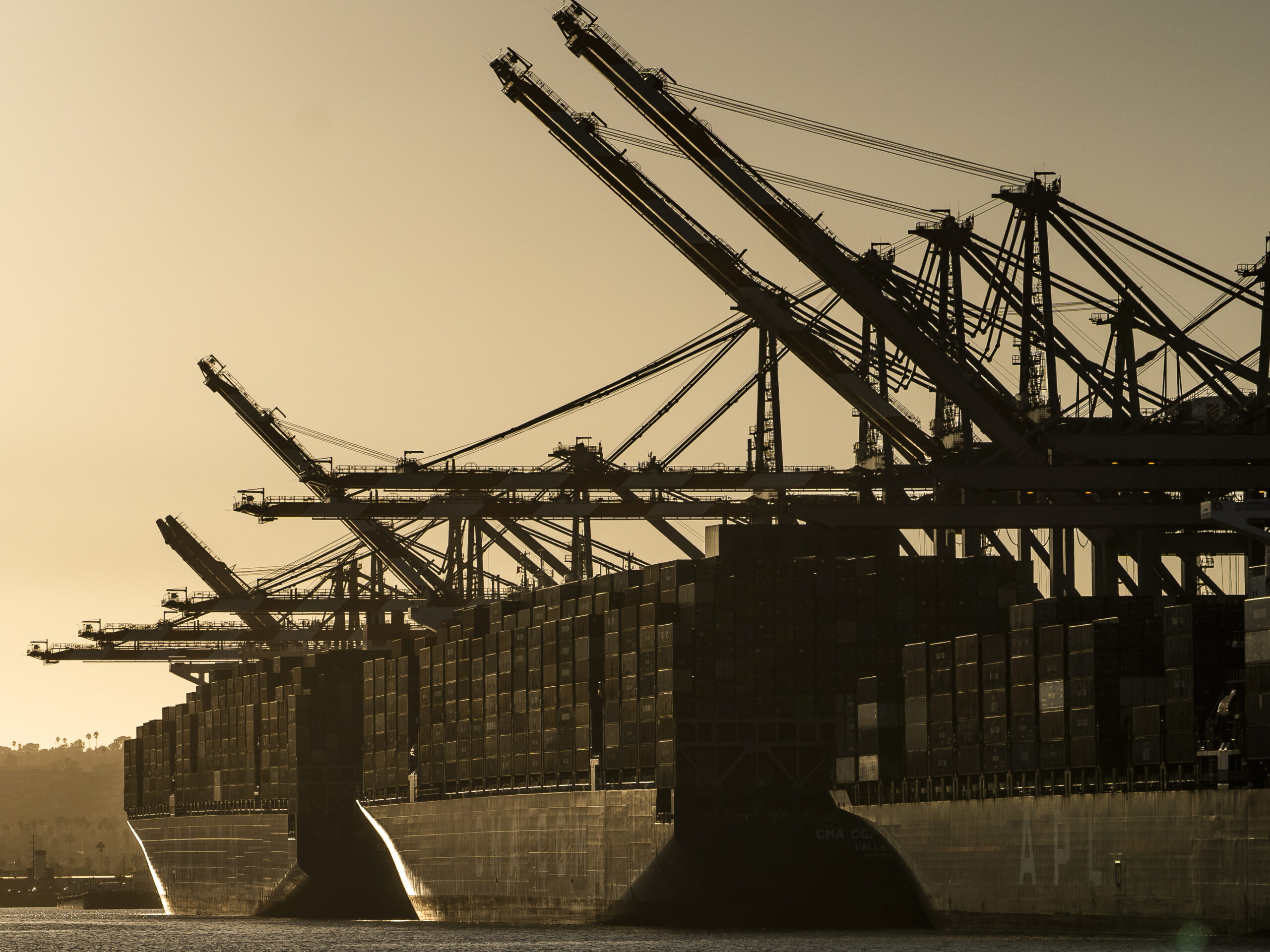
Goods used to be loaded one by one
Before containers, shipping was prohibitively expensive because every piece of cargo had to be loaded on vessels separately.
“On a typical vessel in the 1950s, you might have 200,000 different items … and then each had to be taken out of a ship separately when the ship arrived in port,” Levinson says. “So it took a long time to load and unload a ship. There was a lot of cargo that was damaged. There was a lot of cargo that was lost or stolen.”
In 1956, an American entrepreneur named Malcom McLean used the first modern container ship. He owned a trucking company and was looking for ways to avoid congestion on the highways. McLean came up with the idea of taking the containers off his trucks and putting them on ships.
“His first ship was called the Ideal X. It was a tanker that had been built during World War II,” Levinson says. “The deck was essentially a frame into which the containers could be secured.” That tanker carried just 58 containers.
Containers went overseas a decade later
The first international container ship voyage was in 1966 between Newark, N.J., and Rotterdam in the Netherlands. That changed shipping dramatically. New trade routes formed, special cranes were invented for loading and unloading containers, and bigger and bigger vessels were built.
Janet Porter, editorial board chair of Lloyd’s List, a London-based maritime information service, remembers in 1996 seeing what was then the world’s largest container ship — it could carry 6,000 containers.
“And it was seen as absolutely huge. Barriers had been broken,” Porter says. “And now … they’re just tiddlers,” she says, using a British expression for miniature. “I mean, the biggest ships are about 24,000.”
Now the boxes have additional uses
Containers are used now for more than just shipping. They’re transformed in many parts of the world into makeshift schools, restaurants, clinics and prisons. Architects in wealthier countries are turning them into high-end modular homes.
California-based company Crate Modular, for example, uses containers to make affordable multifamily apartments, temporary housing for people experiencing homelessness and school buildings.
“We procure these empty one-way-trip shipping containers, and then we bring them to our factory in Carson, California,” says the company’s vice president for development, Amanda Gattenby. “We convert them from shipping containers into housing by cutting the sides out, combining them together to make larger spaces, adding steel, putting in plumbing and electrical and drywall.”
The finished apartments are fully insulated and include tiled bathrooms, air conditioning and high ceilings, Gattenby says.
“In the last two years, we’ve produced 432 beds for homelessness and 81 units of affordable housing, as well as some commercial and educational projects, converting over 350 shipping containers into state-approved buildings,” she says.
Supply and demand up the cost
Now during the pandemic, people are buying so many more goods that it’s boosting demand and leading to a shortage of containers, which has sent their prices surging, according to Porter of Lloyd’s List.
She says they went from $1,500 for a 20-foot container and $2,800 for a 40-footer in late 2019, up to $3,000/$5,800 in 2020. Now they are about $4,000/$6,400, but she has seen spot deliveries go as high as $6,000/$8,000.
She expects that the prices will drop once the supply chain crisis ebbs.
“The reason there’s a shortage is because a lot of them are stuck on ships that are waiting outside ports because of this supply chain crisis,” Porter says. And not only does that cause delays for businesses waiting for goods and parts to arrive, but she adds that “those containers can’t be moved back to where they’re needed.”
The shipping containers can’t be unloaded at the docks fast enough to be sent back to Asia, where they’ll be used again to help meet consumer demand.
China, the world’s largest manufacturer of shipping containers, is trying to pick up slack — companies there produced 300,000 containers in September alone, Reuters reported.
But no matter how many there are, the supply chain crisis won’t be solved until the containers are more quickly unloaded and turned around.
9(MDQ2OTU5NjExMDE2MTkwMTE2MDExMzAxYg000))